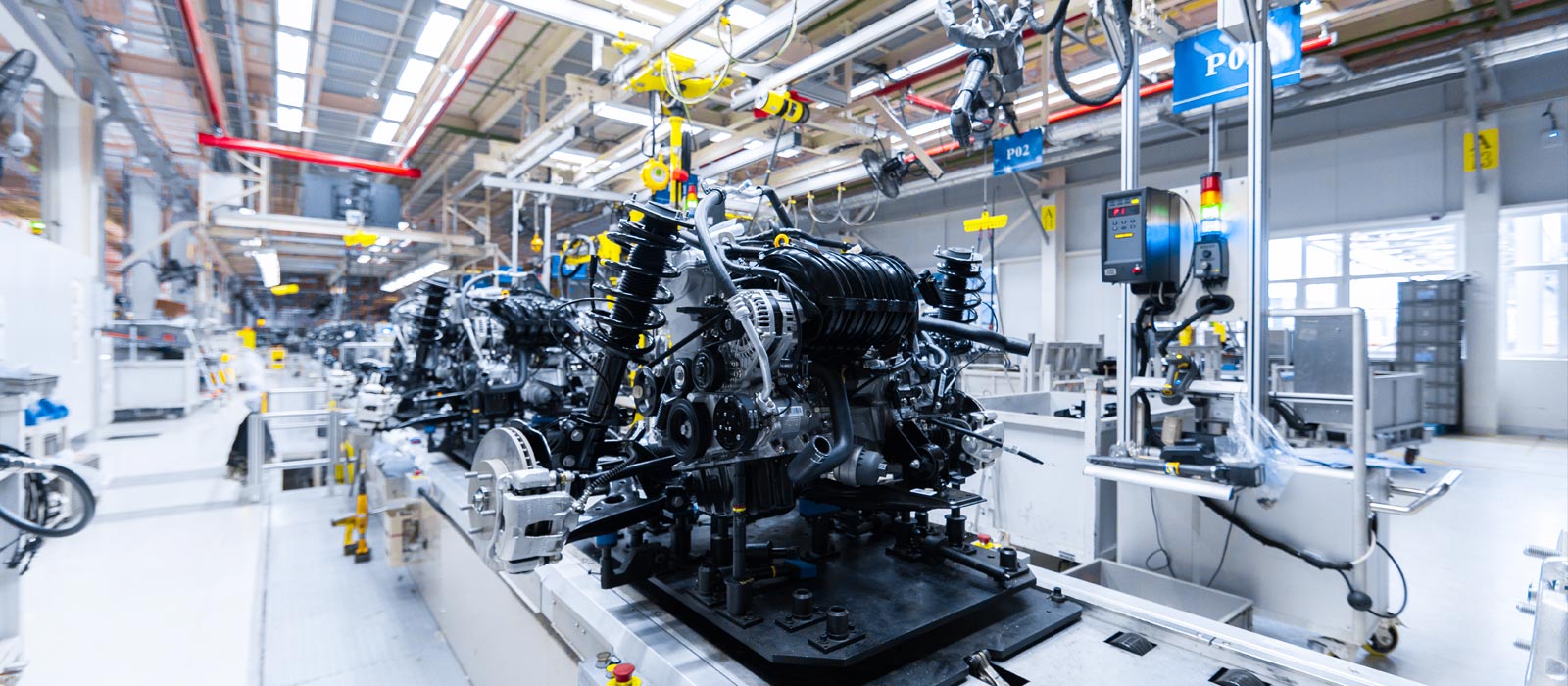
04 Jan Using Cycle Time Analysis to Improve Assembly Line Performance
For a manufacturing entity, improving efficiency means continuous reduction in cycle time for a process. In many cases, cycle time can be improved through the identification and removal of bottlenecks. These bottlenecks can be equipment and/or resource related. Equipment bottlenecks are typically associated with equipment downtime, operator response time, etc. Resource bottlenecks include demand for utilities, labor, and raw materials. Cycle Time Analysis (CTA), supported by machine learning algorithms, is being used to improve assembly efficiency across a wide range of industries.
Bottleneck Identification
CTA can be utilized to identify those bottlenecks that have a significant impact on overall production efficiency of an assembly line. CTA considers various critical parameters: equipment availability, quality rate, Overall Equipment Efficiency (OEE), equipment downtime, operator performance, etc. In addition, CTA can evaluate single machine/operator performance or compare the performance of multiple machines/operators over a designated period. Through CTA, phase durations that are abnormally long compared to historical averages/medians can be flagged, and systematically eliminated.
Cycle Time Benchmarking and Variance Tracking
The first step in CTA is to define the ideal cycle time. The ideal cycle time will be the time required to complete a job with no downtime, no work stoppages, and no flaws. It is critical to analyze ideal cycle times manually to understand the data. Some manufacturing facilities may have real-time data tracking software, such as a material requirements planning (MRP) system, to measure and track cycle time. However, there is no system that can tell you what your ideal cycle times should be. These systems can only report what the cycle time is at any given point in time. They typically do not contain the embedded intelligence necessary to identify your ideal cycle time or to tell you how to get there.
The above concept can be summarized in the following three basic steps:
- Measure your current cycle times. Track your cycle times over multiple shifts and multiple operators. This will help determine the optimum capacity of your assets.
- Drill down into your measurements. Don’t make the mistake of simply relying on your average cycle time as this can provide a false sense of efficiency. This is especially true if there are wide variances in your measurements. Take a deeper look into your measurements to also determine the median and modes within your results. Taking these variances into account will enable you to determine your optimal cycle time.
- Synthesize and analyze your results. Analyze the data you have collected. This can be done manually or via a data-analytics solution. What is causing the variances in your cycle times? Where are the specific bottlenecks that are disrupting your throughput? What is causing those bottlenecks (equipment, materials, operators)? Once these problems have been identified, and corrective actions implemented, your cycle times will decrease, and your output will be more predictable.
Cycle Time and Machine Learning Algorithms
While the ideal cycle time is typically determined manually, machine learning algorithms can be used to automatically identify and analyze deviations and bottlenecks. This process requires training the AI/ML model with real time data gathered during production cycles and quantifying acceptable variances. Once deployed, these models can quickly improve CTA and significantly reduce the time required to spot bottlenecks at different machines/stations.
The implementation of CTA can help manufacturing facilities improve overall production, lower costs, increase quality, reduce downtime, and refine process improvement initiatives. Efforts associated with manual data entry and analysis can be significantly reduced by implementing machine learning models resulting in improved employee efficiency and reduced overhead costs.