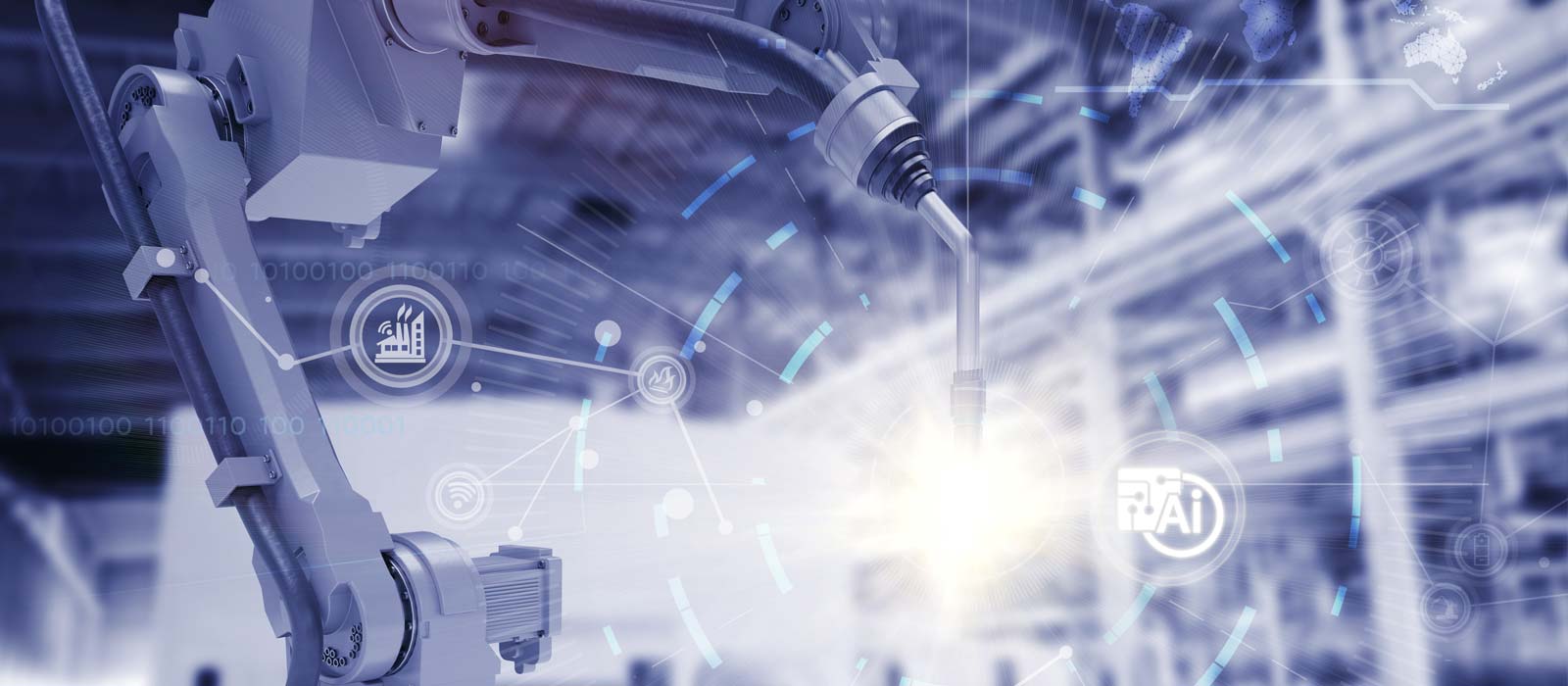
04 Mar MicroAI™ Atom Brings AI to the Wire Mesh Industry
The Business Need
The wire mesh industry relies on a combination of steel looms and human weavers to create wire mesh products. The mesh required by clients can vary in size, density, or type. These varying client requirements can create vastly different efficiencies as some mesh’s are far more difficult for the weavers to work with. Depending on the upkeep of the loom, maintenance issues can also create variances in performance. Minimizing these variances by taking corrective actions would allow industry leaders to operate more efficiently and more cost-effectively.
The Solution
MicroAI’s MicroAI(TM) Atom uses proprietary Artificial Intelligence (AI) and Machine Learning (ML) algorithms to monitor—and learn from—the variances in human and machine behavior. These real-time insights are used to fine tune and normalize variances that negatively impact reliability and production efficiency.
The first step in a typical use case would be to select the appropriate measurements so that the AI engine can gain a proper understanding of the system. Smart devices (motion detectors, electrical monitors, temperature sensors, etc.) could be utilized to monitor performance parameters of the entire ecosystem. Meanwhile, timing measurements could be integrated to track human performance.
The implementation of MicroAI™ Atom would need to incorporate multiple models as the performance of operators and looms can vary widely depending on the specific type of mesh that is being fabricated. This means a management control system would need to be implemented on top of the AI engine to properly shut it off and restart it with the proper models whenever the type of mesh being produced is changed.
The Impact
Once all the required models have been built and enabled, the production line operators, managers, and stakeholders will be provided real-time insights into the normalized performance for each type of mesh being produced. The AI engine, supported by intelligent process workflows, will generate real-time alerts in the event of abnormal machine and/or operator behavior. Tangible benefits to the operation would include the following:
- Transition from reactive machine maintenance to predictive maintenance
- Reduction in machine downtime due to unforeseen breakdowns
- Improved machine capacity and throughputs
- More efficient utilization of machine maintenance staff
- Deeper insights into operator behavior and improved performance
- Longer asset lifespans, more efficient human interaction, reduced costs, and improved ROI.
MicroAI™ Atom is bringing Endpoint AI to a whole host of manufacturing operations looking to transition into Industry 4.0. The wire mesh industry is just one example of how increased intelligence can completely transform a legacy operation into a “smart” operation.