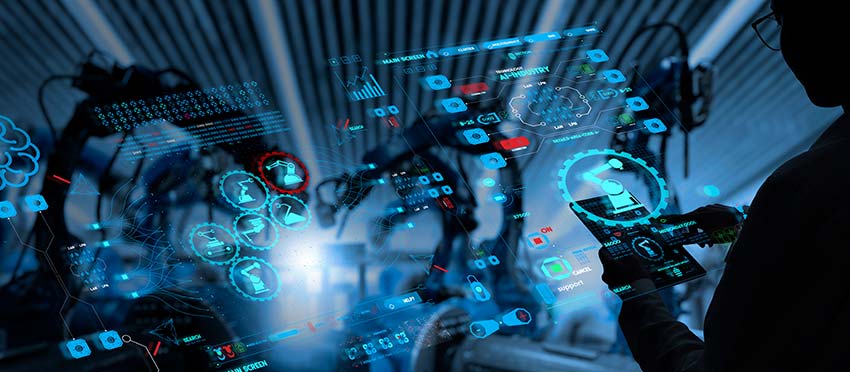
30 Sep Industry 4.0 – Implications & Benefits for Manufacturing
Industry 4.0 (the Fourth Industrial Revolution) has evolved from a niche concept to a full-fledged, legitimate, revolution. Industry 4.0 now has significant implications for manufacturing operations around the globe. Industries that are slow to adapt will find it increasing difficult to compete in an increasingly competitive marketplace.
Industry 4.0 Defined
Industry 4.0 is characterized as the Fourth Industrial Revolution. It is generally considered to be an extension of the Third Industrial Revolution that occurred during that closing years of the 20th century. The Third Industrial Revolution laid the groundwork for the levels of digital transformation and automation that are the primary characteristics of Industry 4.0 initiatives.
Industry 4.0 combines advances in artificial intelligence (AI), machine learning (ML), and the industrial internet of things (IIoT) to enable accelerated advancements in real-time intelligence and automation. “Smart Manufacturing” is no longer just an ambiguous buzz-phrase or a futuristic concept. Industry 4.0 initiatives are powering transformative developments in the areas of asset management, process automation, quality improvement, cost reduction, and more.
A Pathway to Operational Excellence
“Operational excellence” has always been a relative term. Excellent compared to what? Excellent compared to who? Business conditions are changing. Nowhere is this more evident than within the manufacturing segment. The attainment of true operational excellence is now an imperative to competitiveness. Industry 4.0 is providing the backbone to fundamental change in the ways that manufacturers operate. Primary examples would include:
Holistic Connectivity: Siloed points of intelligence provide limited benefit to the manufacturing operation. Disconnects between assets and processes cripple an operation’s ability to attain—and maintain—real-time visibility into the performance of the entire manufacturing process.
Industry 4.0, via the use of Edge-native AI technology, allows for AI and ML to be embedded into every mission-critical asset and process. This dynamic and scalable methodology creates an intelligent ecosystem that is completely interconnected.
- Connected machines
- Connected devices
- Connected processes
Predictive Analytics: The manufacturing sector has been using advanced data analytics for decades. The automation of the data collection process has allowed stakeholders to analyze that data and determine appropriate courses of action. The problem is that the process has been purely reactive. Corrective actions are too often implemented after significant losses to productivity or quality have already occurred.
Predictive maintenance is the cornerstone of Industry 4.0. Predictive analytics drive predictive maintenance. Edge-native AI embeds and trains AI models directly onto the microcontroller (MCU) of individual devices or machines. This eliminates the problem of poor visibility into real-time asset health and performance.
- Transition from reactive to predictive maintenance
- Reduction in downtime of critical assets
- More efficient use of maintenance personnel
Asset Optimization: For machine-intensive operations, Overall Equipment Effectiveness (OEE) is a high-priority KPI. Historically, an OEE score of 75% was considered acceptable. That is no longer the case. To gain competitive advantage, manufacturers are now looking for ways to reach scores of 95%.
Industry 4.0 programs, utilizing Endpoint AI solutions like MicroAI AtomML, are building transformative capabilities to create predictive models that operate locally and in real time. This extreme-edge approach allows machine performance data to be collected, analyzed, and stored within the local environment.
- Deeper asset performance insights
- Faster analysis and quicker corrective actions
- Fine-tuning of operational parameters via ML algorithms
- Less reliance on human intervention
- Higher OEE scores
Process Intelligence: The need for control of manufacturing processes has moved well beyond what legacy process management solutions can provide. Manufactures now need to be able to implement processes that learn, evolve, and adapt. This requires a paradigm shift in process automation/management technology.
AI-enabled “intelligent” workflows represent the next generation in process management capability. This is process management that can be embedded directly into assets within the manufacturing ecosystem. Intelligent workflows are self-learning and self-adjusting. They bring a level of real-time process control and micromanagement that had not been previously possible.
- Easily embedded and modeled
- Self-learning and self-adjusting
- Real-time process control with minimal intervention
Operational Costs: A few things never change. The need to control production costs is one of those constants. Being able to compete in a hyper-competitive marketplace requires an ability to squeeze costs without sacrificing the quality of products or services. The difference between success and failure can be razor thin.
Industry 4.0 brings enhanced cost-saving opportunities to the manufacturing environment. Edge-native AI technology is being deployed as an alternative to traditional cloud-based AI solutions. This has effectively reduced the cost of AI-entry and provides several first and second-level cost advantages.
- Reduction/elimination in cloud storage and processing costs
- Reduction in the amount of support hardware
- Extension in lifespan of expensive assets
- Improved yields and reduction in scrap costs
- More efficient utilization of human resources
The Fourth Industrial Revolution show no signs of losing momentum. As new supportive technologies continue to be developed, Industry 4.0 initiatives will continue to proliferate across the manufacturing landscape. The implications for adopters are clear. Implications for non-adopters are also clear.